Robotics automation equipment play a vital role in production and assembly lines in manufacturing, food processing and pharmaceutical facilities globally. As innovative new products emerge these global manufacturers frequently move production of existing products to other plants internationally to free up production space and capacity for new production lines.The safe transportation of these high value pieces of robotics equipment internationally is critically important. These sensitive machines need to arrive at their new manufacturing base in perfect condition ready to be installed in another production line. This is an example of when manufacturers call on the Cronin Movers team to design bespoke crating with moisture barriers to transport their sensitive equipment.
WHAT WAS INVOLVED
Our specialist surveyor carried out a site survey of the robotics automation equipment to be crated and transported. This includes careful consideration of the logistics of safely moving and positioning the equipment in a suitable area for crating.
Detailed measurements were taken of the equipment and these measurements were used on our specialist crate manufacturing software.
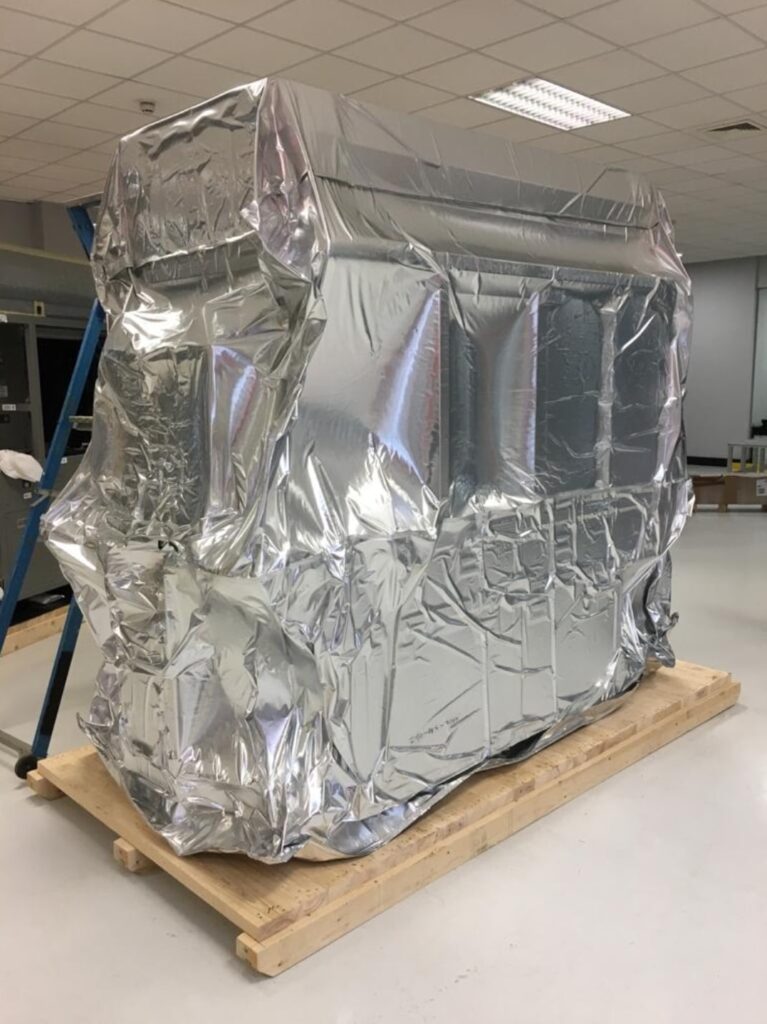
Crates are designed specifically for each task to ISPM15 standards including the addition of PP007 moisture protection barrier foil bags, an additional lair of protection for a long ocean vessel journeys. All of our crates are manufactured in our workshop and transported flat packed to the required site location.
The crate base was placed in the designated crating location and the moisture protection ground sheet was placed on the base. The robotics equipment was carefully moved and positioned on the ground sheet and secured to the base of the crate.
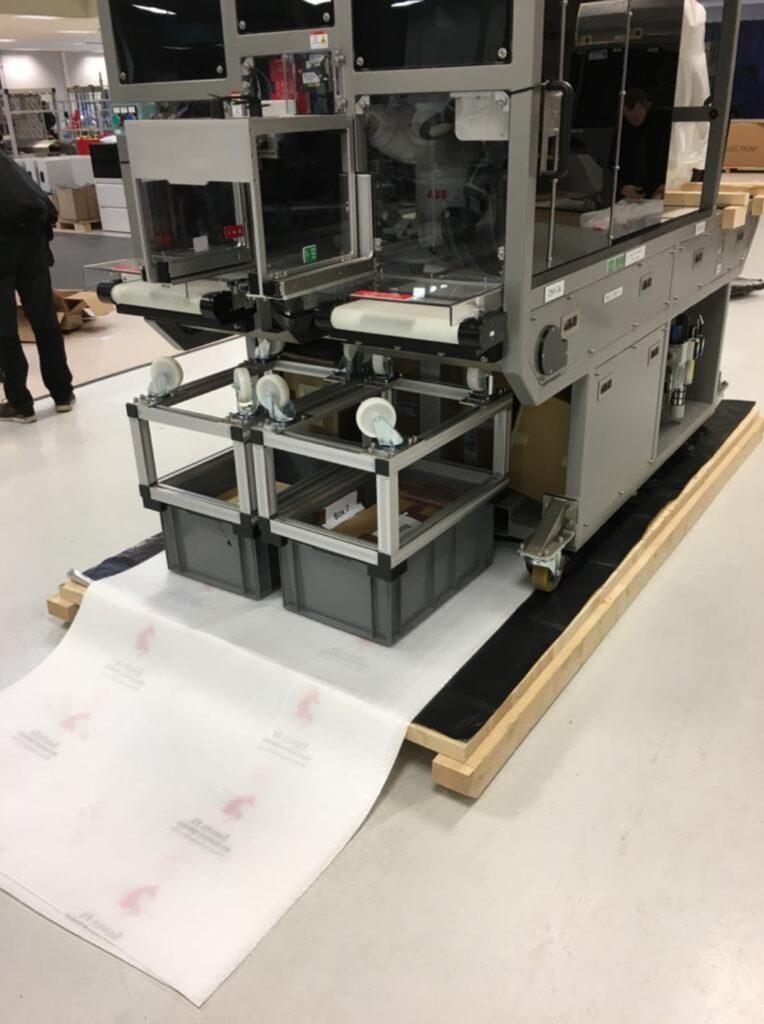
Once secured to the base the purpose made moisture protection bag was placed over the machine and heat sealed to the ground sheet using a crimping heat iron. The remaining air inside the moisture protection bag was extracted using a vacuum before being finished sealed.
At this point the crating walls were set and secured in place around the machine and the top of the crate was secured to the walls. Finally the crate was fully sealed.
THE OUTCOME
Using a stencil template, the outside of the crate was marked up with all the required shipment details. For completeness we also add the crate dimensions, weights and, for ease of offloading, mark the point of centre of gravity.
The finished crates were loaded and secured into a 40ft HC drylined container for onward transportation.
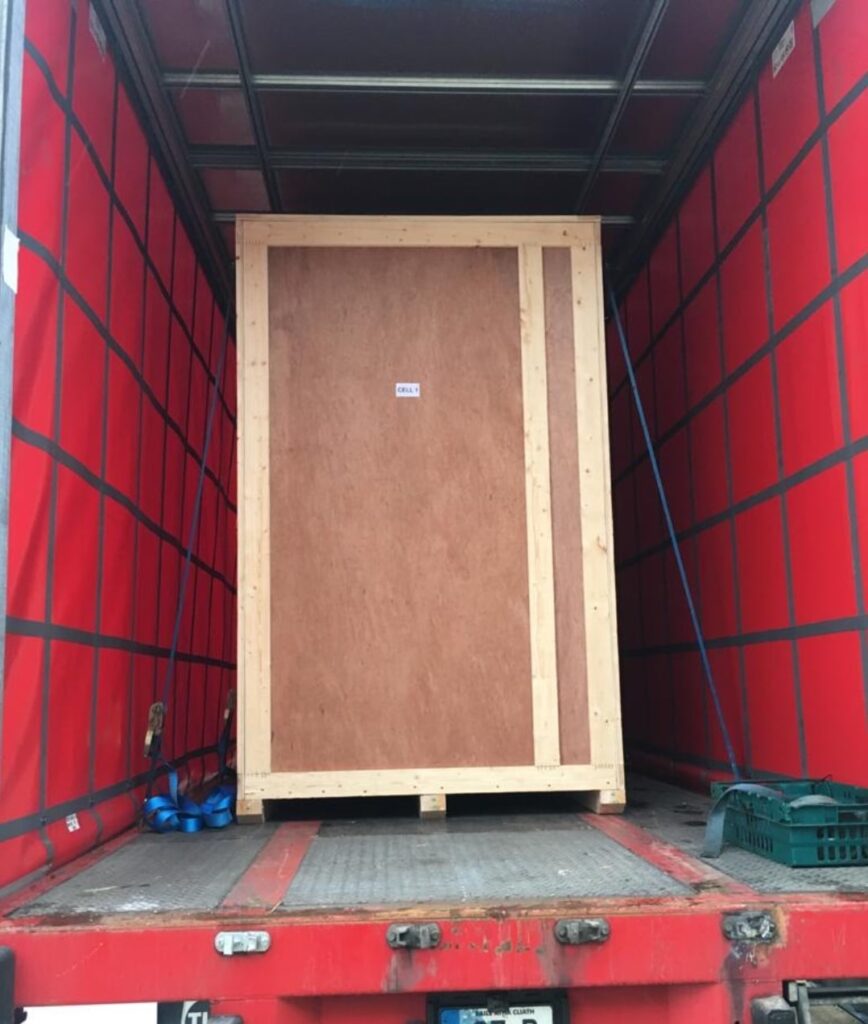
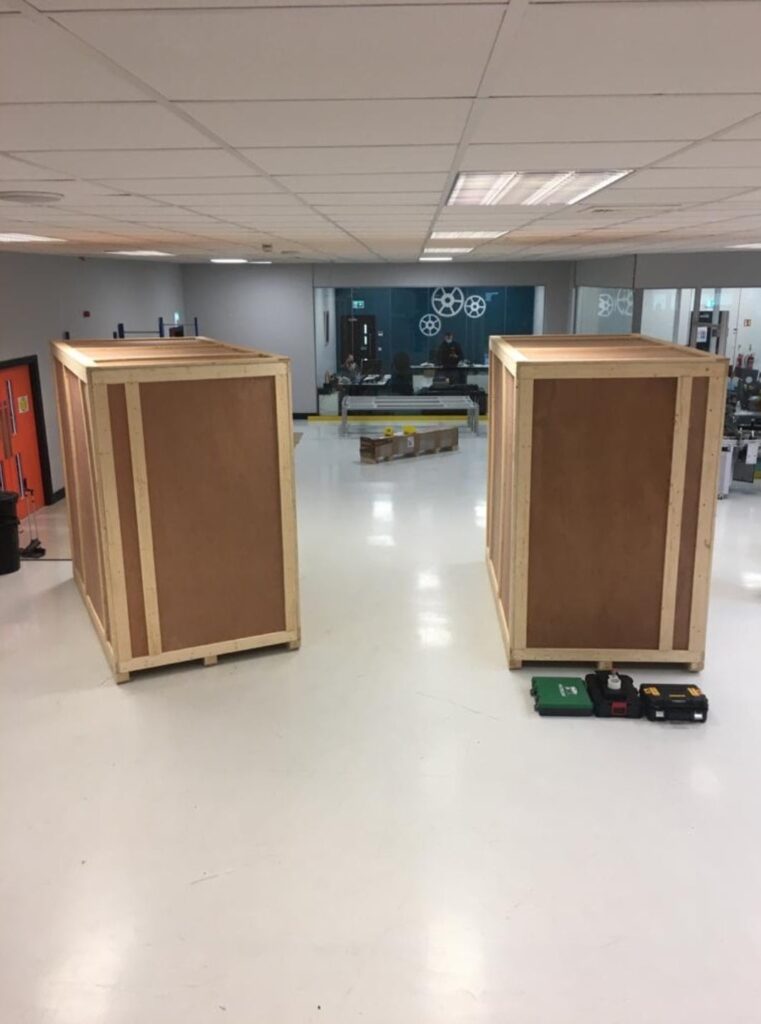
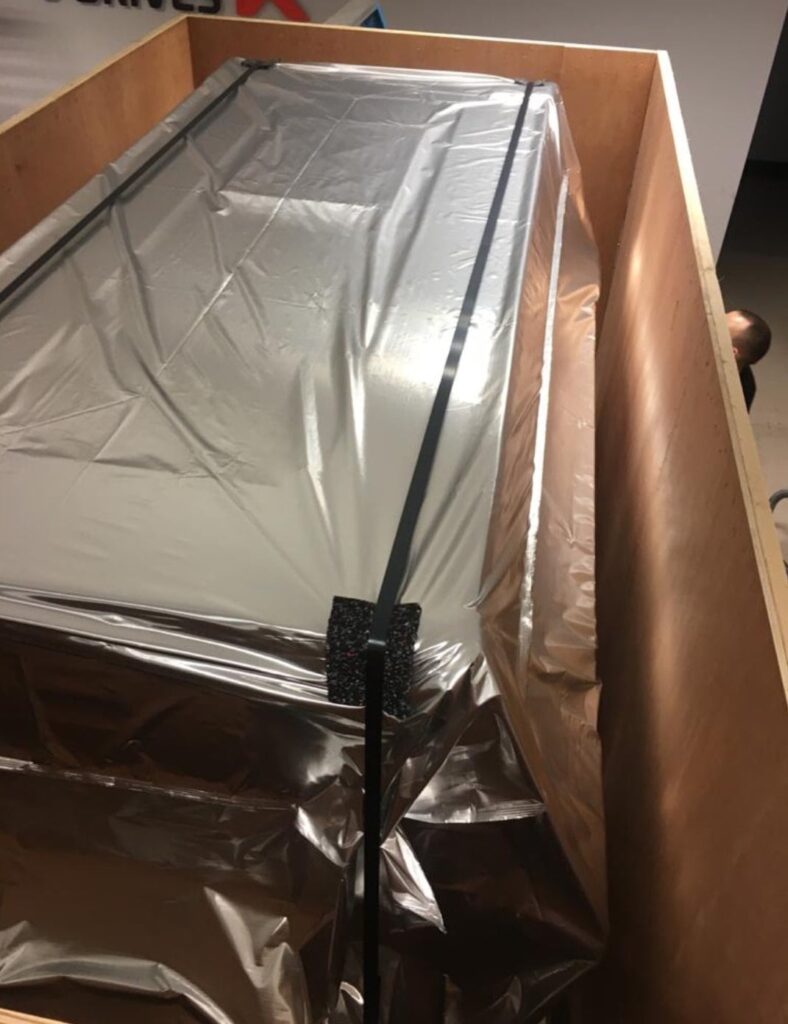
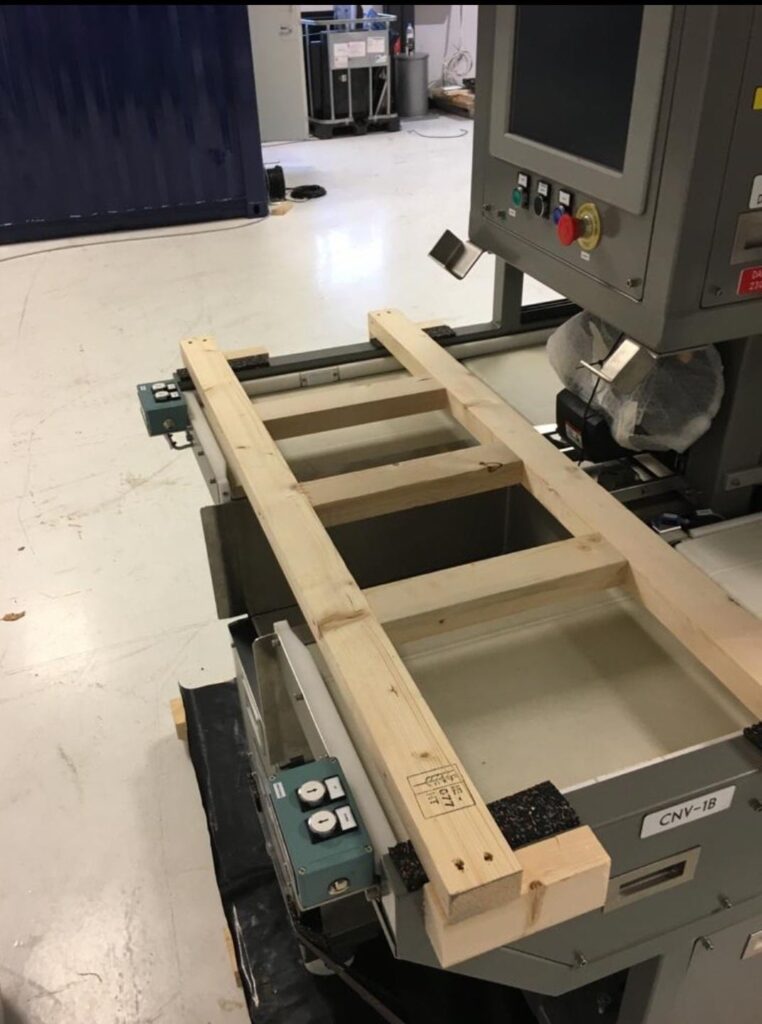