This Machinery Movers project involved a robotics automation line move in a pharmaceutical production facility for Robotics and Drives (an industrial robotics and automation company based in Mullingar, Ireland). They required a Machinery Moving specialist with experience of handling pharmaceutical production equipment to provide the necessary expertise to pack, crate and ship the robotics production line equipment to Japan for a major global Lifesciences company.
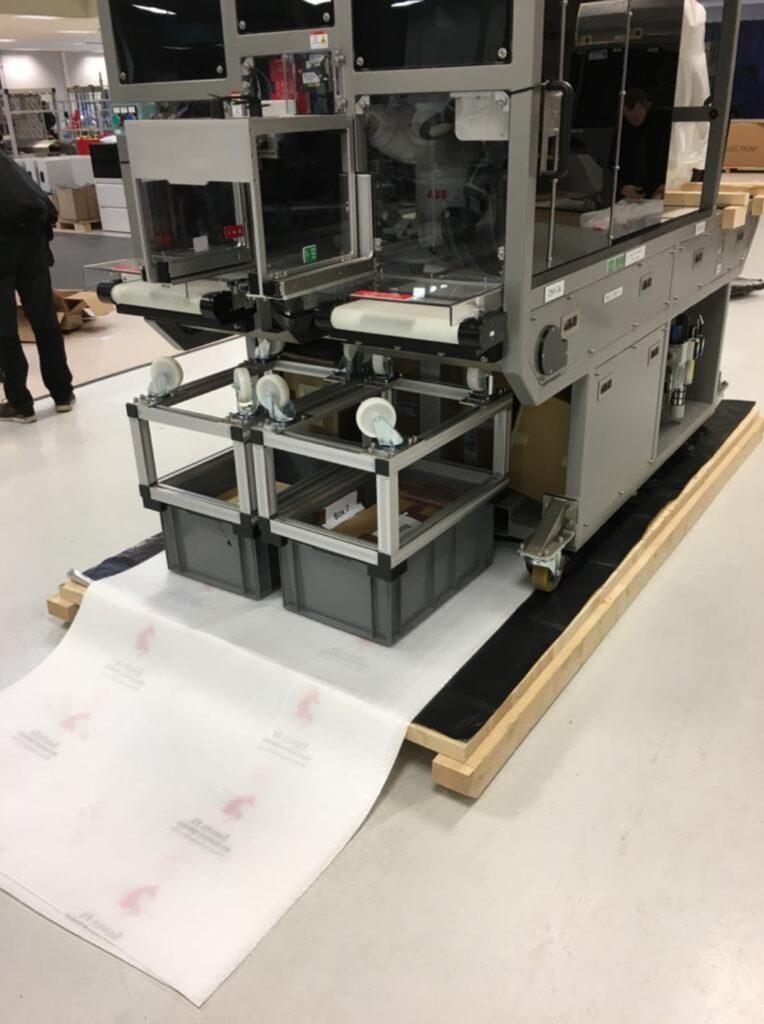
WHAT WAS INVOLVED
This robotics automation line move in a pharmaceutical production facility was an important relocation of high value equipment that required detailed project planning, project management, professional rigging and transportation. The Cronin Movers Machinery Moving Team’s experience of working in clean room pharmaceutical production environments was critical to the planning and execution of this machinery move, with the team leader reporting directly to the Robotics and Drives on-site project manager.
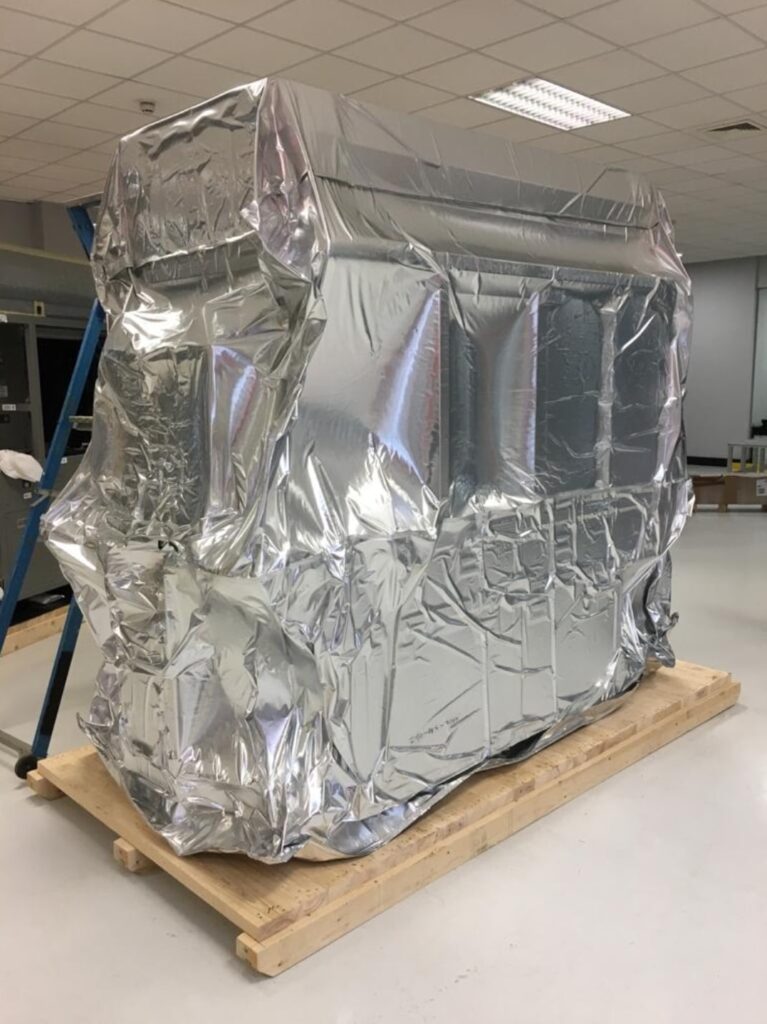
The project involved the separation of the production line equipment and each section of machinery was carefully moved to a pre-prepared staging area. The machinery was placed on a purpose built base, before being wrapped and vacuumed sealed in specially manufactured moisture protection barrier foil bags, for protection while in transit.
Each piece of equipment was then secured to the base before being over cased and sealed in a purpose built timber crate. Once all identification and destination details were marked on the outside of the crates they were carefully loaded onto the awaiting transport vehicle to begin the journey from Mullingar to Japan.
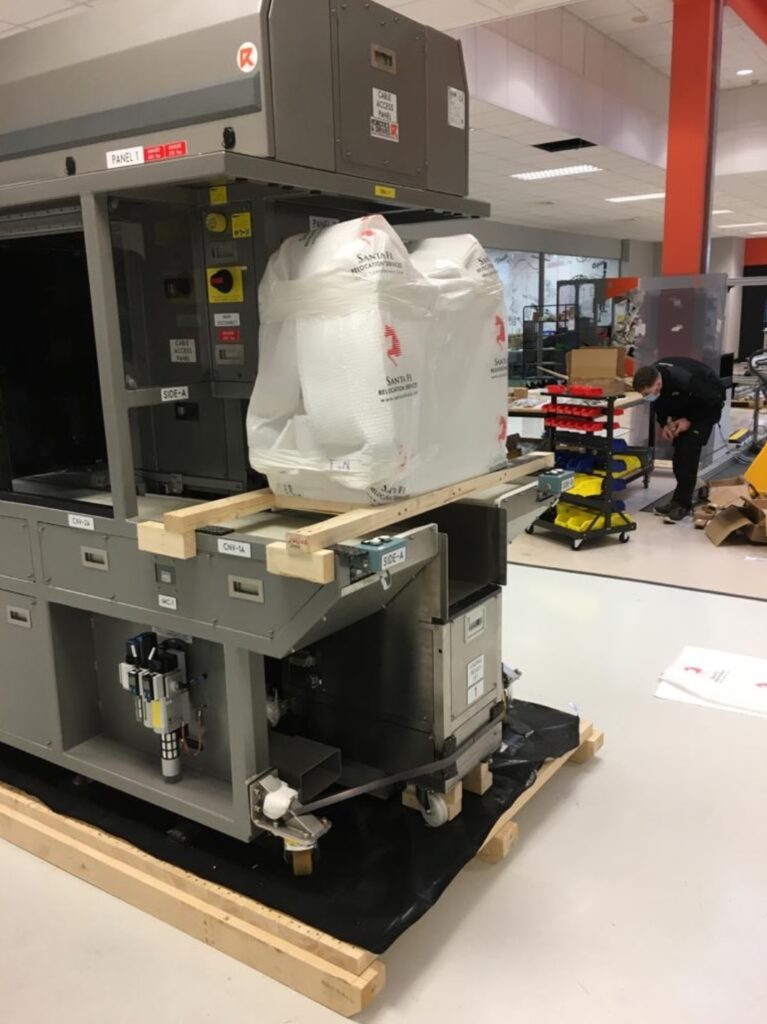
On arrival in Japan each crate was offloaded in the order required, de-crated, unpacked and skated to its final position. The line assembly team reconnected all the sections of machinery to ensure the production line was complete and ready for testing.
THE OUTCOME
This robotics automation line move in a pharmaceutical production facility was completed successfully. Following a thorough risk assessment, the decommissioning, separation of the production line equipment, removal, packing/crating, loading and transportation of the machinery to Japan was completed on time and within the agreed budget.
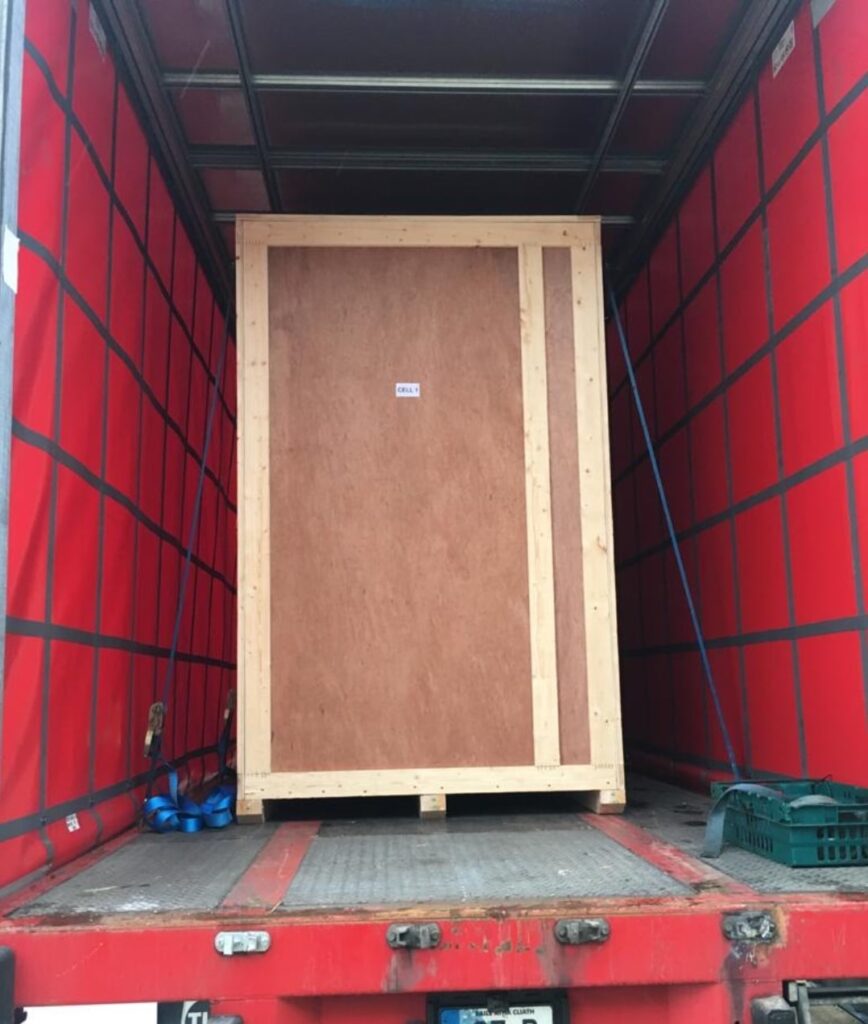